How to Handle Customer Complaints Professionally: A Comprehensive Guide
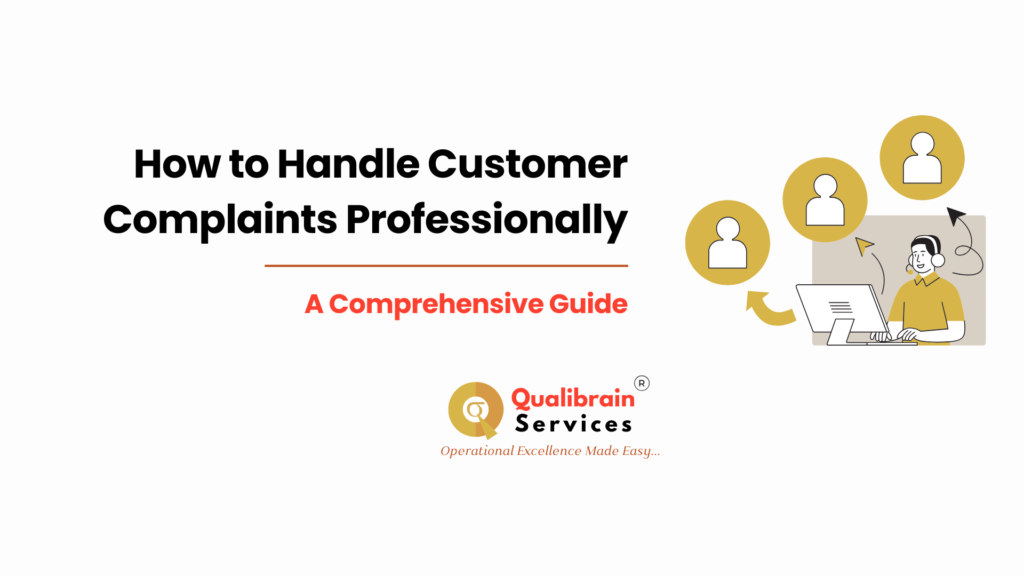
Introduction Handling customer complaints professionally is essential for maintaining customer trust, improving business processes, and ensuring long-term success. When managed effectively, complaints can serve as valuable feedback that drives product and service enhancements. This guide explores proven strategies, key principles, and advanced techniques to help organisations handle customer complaints professionally and enhance customer satisfaction. The Importance of Professional Complaint Handling Customer complaints provide businesses with an opportunity to refine their services, address pain points, and build stronger relationships. A well-handled complaint can turn a dissatisfied customer into a loyal advocate. Why Effective Complaint Management Matters: Research shows that businesses investing in structured complaint management see increased profitability and stronger customer relationships. Key Principles of Effective Complaint Management To handle customer complaints professionally, organizations should adopt the following core principles: Step-by-Step Strategy for Handling Customer Complaints Tools & Techniques for Superior Complaint Management Effective complaint handling requires the right tools and methodologies: Essential Tools: Proven Techniques: Overcoming Challenges in Complaint Handling Even with the best strategies, challenges can arise. Here’s how to address common obstacles: 1. Communication Gaps 2. Resource Constraints 3. Resistance to Change 4. Inconsistent Processes Future Trends in Customer Complaint Management The landscape of complaint management is evolving. Businesses must stay ahead by embracing emerging trends: How to Stay Ahead: How Qualibrain Services Helps Organizations Manage Customer Complaints Professionally At Qualibrain Services, we specialize in equipping businesses with the tools and expertise to handle customer complaints professionally. Our customized solutions ensure that organizations transform challenges into opportunities for growth and excellence. Our Key Offerings: Benefits of Partnering with Qualibrain Services: ✔ Enhanced customer satisfaction and loyalty✔ Improved operational efficiency and process standardization✔ Data-driven insights to refine business strategies✔ Competitive advantage through superior complaint resolution Let’s transform customer complaints into opportunities for excellence. Contact Qualibrain Services today to optimize your complaint management process and build a stronger, customer-centric business. Conclusion Handling customer complaints professionally is not just about damage control—it’s about creating a sustainable, customer-focused business model. By implementing structured complaint management strategies and leveraging technology, organizations can foster long-term customer loyalty and operational excellence. For organizations looking to elevate their approach, Qualibrain Services provides expert guidance, training, and consulting solutions that drive real results. Every complaint is an opportunity for improvement—let’s make the most of it.
Breaking Through Career Saturation: Strategies for Quality Professionals

Breaking Through Career Saturation: Strategies for Quality Professionals As a quality professional, you start your career with passion, eager to implement quality systems and drive improvements. However, after a few years, you may find yourself in a rut—stagnant, uninspired, and unsure about the next step. This phase, known as career saturation, is common. The good news is that you can break through it. At Qualibrain Services, we have helped countless professionals rejuvenate their careers and achieve greater heights. Let’s explore how you can overcome career stagnation and rediscover your professional growth path. Recognizing Career Saturation: Are You Stuck? Before tackling career stagnation, it is essential to identify if you are experiencing it. Here are some telltale signs: Signs of Career Saturation in Quality Management Signs What It Looks Like Feeling Unchallenged Every day feels like a routine with no exciting challenges. Lack of Motivation Work no longer excites you as it once did. Limited Growth Opportunities No clear career advancement paths in sight. Burnout & Stress Constant exhaustion, frustration, and lack of enthusiasm. Stagnant Skillset No new learning, just repeating the same processes. If you relate to two or more of these signs, you may be facing career saturation. However, there are actionable strategies to reignite your career. 1. Embrace Continuous Learning & Upskilling The quality management field is evolving. Are you? Many professionals reach a saturation point because they stop learning. To stay ahead, you must continuously upgrade your skills. Effective Ways to Upskill in Quality Management Professionals with continuous learning habits earn 30% more on average than those who do not. 2. Find a Mentor & Build a Strong Network Having a mentor can be a game-changer. A mentor provides guidance, insights, and opens doors to new opportunities. How Mentorship Helps: Pro Tip: Join professional groups like ASQ (American Society for Quality) or ISPE (International Society for Pharmaceutical Engineering) to find mentors and network. 3. Set Clear Career Goals & Make a Plan Many professionals hit a plateau simply because they do not have a structured career plan. Without goals, your career drifts aimlessly. SMART Career Goal Framework Criteria Example Goal Specific Earn a Six Sigma Black Belt in 12 months. Measurable Complete five projects using Six Sigma tools. Achievable Dedicate five hours per week for study and practice. Relevant Helps in getting a leadership role in quality management. Time-bound Achieve the goal within one year. 4. Consider Lateral Moves & New Challenges If promotions seem distant, consider a lateral career move—a shift into a new role that builds new skills and experiences. Benefits of Lateral Moves: Example: A Quality Engineer transitioning into a Process Improvement Manager role learns Lean and Six Sigma implementation, making them a strong candidate for future Operational Excellence Director roles. Career Path Progression (From Quality Engineer to Leadership) Quality Engineer → Senior Quality Engineer → Quality Manager → Operational Excellence Leader → Director of Quality 5. Improve Work-Life Balance & Prevent Burnout Work stress can lead to frustration and saturation. Maintaining a healthy work-life balance ensures long-term career motivation. Tips to Improve Work-Life Balance: 76% of professionals who practice work-life balance report higher job satisfaction and better career longevity. 6. Leverage Professional Development Resources Many professionals remain stuck because they do not use available career development resources. Here is what you can do: 7. Explore Entrepreneurship & Consulting Opportunities If traditional career paths seem unfulfilling, why not create your own opportunities? Many quality professionals transition into freelance consulting or entrepreneurship in process improvement and compliance auditing. Possible Entrepreneurship Avenues: Conclusion: Take Charge of Your Career Today Career saturation is not the end—it is a signal for change. With the right strategies, you can reignite your passion and accelerate your professional growth. Quick Recap of Strategies: At Qualibrain Services, we empower professionals with training, consulting, and executive recruitment services to help them break barriers and achieve global competitiveness. Ready to reignite your career? Connect with us at Qualibrain Services to explore our expert-led career development programs and training opportunities. Your next breakthrough is just one step away. Take it now. Did this article help you? Share it with fellow professionals who need a career boost.
Unlocking Automotive Excellence: The Comprehensive Guide to VDA 6.3 Implementation and Its Benefits
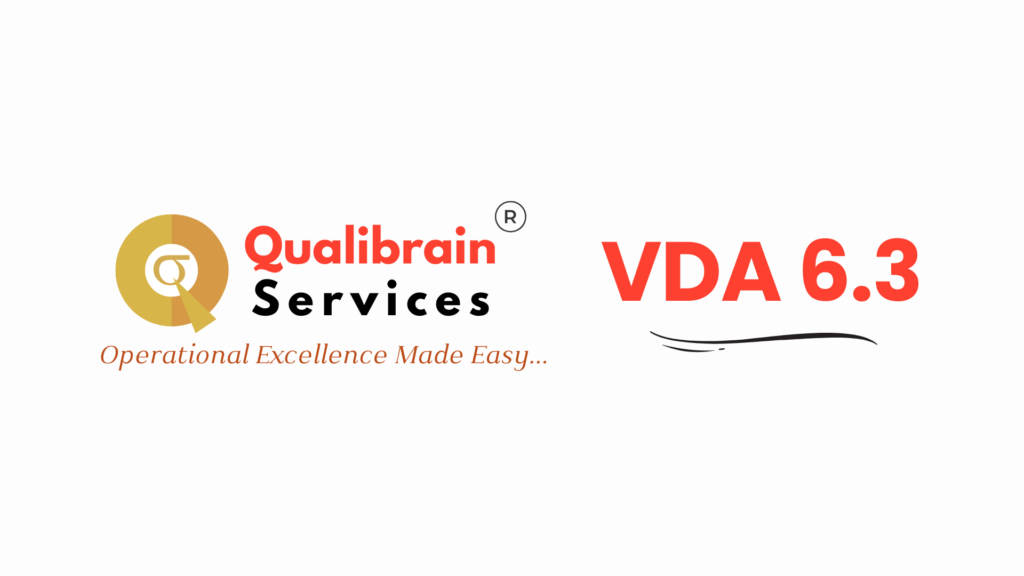
VDA 6.3 In today’s fiercely competitive automotive industry, ensuring the highest quality across manufacturing and service processes is not just a goal—it’s a necessity. With ever-increasing demands for reliability, safety, and efficiency, companies are constantly looking for ways to streamline operations, reduce defects, and deliver superior products. One of the most robust solutions available is the VDA 6.3 process audit standard. Developed by the German Association of the Automotive Industry (VDA), VDA 6.3 provides a systematic framework to evaluate, monitor, and improve process quality throughout the automotive supply chain. This comprehensive guide delves into what VDA 6.3 is, outlines its implementation steps, and highlights the numerous benefits it brings to automotive organizations—all backed by industry statistics, trends, and real-world examples. What is VDA 6.3? VDA 6.3 is a quality management and process audit standard that focuses on evaluating the efficiency and effectiveness of processes within the automotive industry. Unlike traditional quality control measures that concentrate solely on end-product inspection, VDA 6.3 delves deep into the processes that produce those outcomes. By auditing these processes, organizations can identify root causes of inefficiencies, ensure compliance with industry standards, and drive continuous improvement. The Seven Process Elements At the heart of VDA 6.3 are the seven process elements (P1–P7), which cover every stage of the product lifecycle—from project planning and development through to production, service, and aftermarket processes. This structured approach ensures that quality isn’t an afterthought but an integral part of the entire production process. The elements include: These elements provide a roadmap for organizations to scrutinize and enhance every facet of their operations. The Strategic Importance of VDA 6.3 in the Automotive Industry The automotive sector is synonymous with precision and reliability. A single process defect can lead to costly recalls, production downtime, and a tarnished brand reputation. VDA 6.3 addresses these challenges head-on by providing a robust mechanism for risk assessment and process optimization. Key Statistics and Industry Insights These numbers underscore the transformative potential of VDA 6.3 in driving operational excellence and securing a competitive edge in the automotive industry. Detailed Steps for Implementing VDA 6.3 Implementing VDA 6.3 is a strategic initiative that requires careful planning, rigorous training, and ongoing monitoring. The following steps outline a comprehensive approach to successfully integrate VDA 6.3 into your organization. 1. Preparation and Training Auditor Certification and Skill Development Building Internal Awareness 2. Process Mapping and Gap Analysis Identifying and Documenting Key Processes Leveraging Data Analytics 3. Conducting Process Audits Utilizing Standardized Audit Tools Supplier Evaluations 4. Implementing Corrective Actions Addressing Non-Conformities Establishing a Continuous Feedback Loop 5. Monitoring and Continuous Improvement Regular Audit Cycles Integrating Digital Tools Benchmarking and Best Practices The Tangible Benefits of VDA 6.3 Implementation Implementing VDA 6.3 is more than just a compliance exercise—it’s a strategic initiative that delivers measurable benefits. Here, we delve into the key advantages of adopting VDA 6.3, reinforced with concrete numbers and real-world examples. 1. Enhanced Process Quality Reduction in Defects and Rework 2. Improved Risk Management Proactive Risk Identification 3. Strengthened Supplier Relationships Ensuring Consistent Quality Across the Supply Chain 4. Increased Customer Confidence and Market Reputation Building Trust Through Demonstrable Quality 5. A Competitive Edge in a Global Market Strategic Business Growth and Innovation Integrating Technology with VDA 6.3 The Role of Digital Tools in Modern Quality Management Digital transformation is revolutionizing the way organizations manage quality. The integration of digital tools with VDA 6.3 not only enhances the efficiency of audits but also provides real-time insights into process performance. Digital Audit Management Systems Data-Driven Decision Making Future Trends in Quality Management As the automotive industry evolves, the role of emerging technologies like artificial intelligence (AI) and machine learning (ML) in quality management is set to grow. These technologies will further enhance predictive maintenance, defect detection, and process optimization, positioning companies that embrace them at the forefront of the industry. Overcoming Challenges in VDA 6.3 Implementation While the benefits of VDA 6.3 are clear, its implementation is not without challenges. Understanding and addressing these obstacles is essential for reaping the full benefits of the standard. Cultural Change and Employee Buy-In Integrating with Existing Systems Continuous Monitoring and Adaptation Conclusion: Driving Towards Operational Excellence Implementing VDA 6.3 is much more than a compliance exercise—it is a strategic initiative that drives operational excellence, reduces risk, and enhances market competitiveness. Through systematic process audits and continuous improvement, automotive companies can achieve measurable benefits such as up to a 30% reduction in defect rates, productivity boosts of 15-20%, and significant improvements in supply chain reliability. These tangible benefits are reflected in real-world success stories and reinforced by modern data-driven practices and digital transformation. Whether you are a large-scale manufacturer or a Tier 1 supplier, adopting VDA 6.3 positions your organization to thrive in a competitive global market, enhance customer trust, and drive sustainable growth. About the Author Charudatta Atrey VDA Certified Trainer and Consultant, Founder of Qualibrain Services Charudatta Atrey is a seasoned expert in automotive quality management and process optimization. With years of hands-on experience and a passion for excellence, Charudatta has empowered numerous automotive organizations to implement VDA 6.3 successfully, resulting in significant improvements in quality, efficiency, and customer satisfaction. Ready to Transform Your Quality Management? At Qualibrain Services, we specialize in VDA 6.3 training and consulting, designed to help your organization achieve unparalleled quality standards. Are you ready to embark on the journey toward operational excellence? Contact us today to learn more about our VDA 6.3 training programs and discover how we can help you unlock the full potential of your quality management system. For more information or to schedule a training session, reach out to us at charudatta.atre@qualibrain.in or visit our www.qualibrain.in By embracing VDA 6.3, you are not only enhancing your processes but also positioning your company as a leader in the automotive industry. The road to success is paved with quality, and with VDA 6.3 as your roadmap, the future of automotive manufacturing looks brighter than ever. Let Qualibrain Services guide you on this transformative journey.